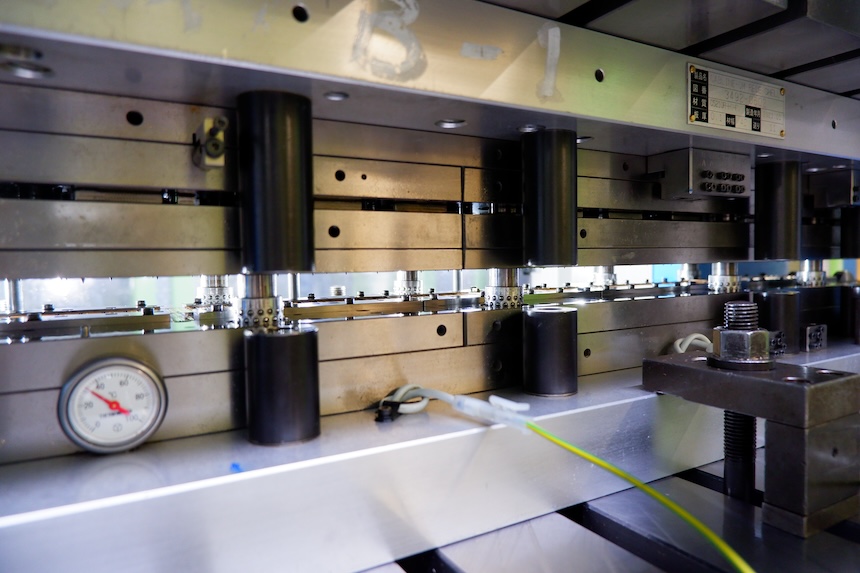
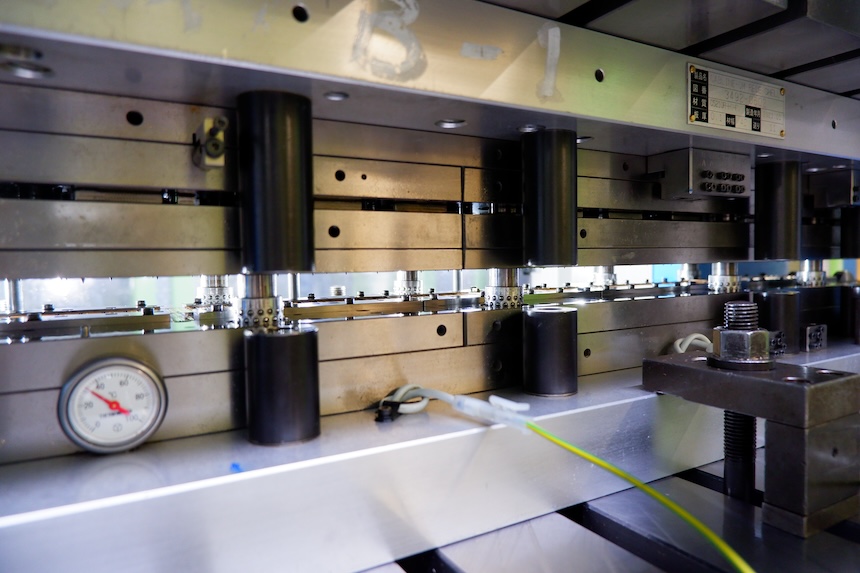
Ichimura Seisakusho successfully uses Agathon roller guides
The medium-sized company Ichimura Seisakusho (Uenohara City, Japan) is a manufacturer of electromechanical precision parts. Its main products are terminal blocks and switches for automobiles, household appliances and computers, as well as other products that require precision in the micrometer range. The necessary high-performance tools for progressive presses are developed and manufactured in-house. Frequent quality problems were solved by changing the guide elements to Agathon roller guides.
The core of Ichimura Seisakusho's corporate philosophy is that the company assumes overall responsibility for the process chain from tool manufacture to large-scale production. In order to better fulfill customer requirements, improvements in the areas of production and customer service are actively pursued.
Mass production of micro connectors on high-speed presses
Since its founding in 1965, the company has been continuously active in the production of electronic components on progressive presses. The high-performance tools required for this are manufactured in the company's own tool shop. The original main products were switch parts for electric toys and pocket calculators. For a time, the focus was on slide switches, for which a separate brand was even introduced. Solutions for automated production were developed for this purpose. Due to changing market requirements, the focus later shifted to the manufacturing of precision electronic components such as connectors. For this purpose, technologies were developed to reliably produce large quantities of board-to-board connec3
tors, e.g. for smartphones, with the help of high-speed presses. «We have a track record of millions of contacts per month for some tools», says Shinji Omata, Head of Design in the Development Department. In 2021, the company achieved IATF 16949 certification, the international quality management standard for the automotive industry. Since then, this market has been supplied with a range of different components.
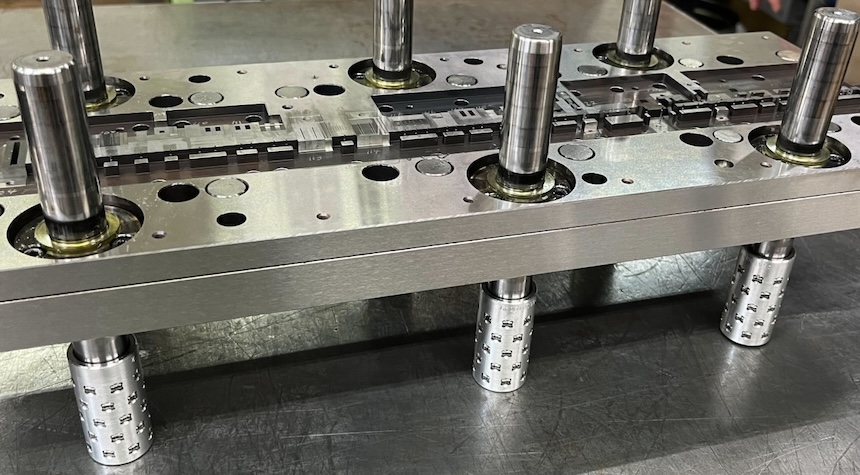
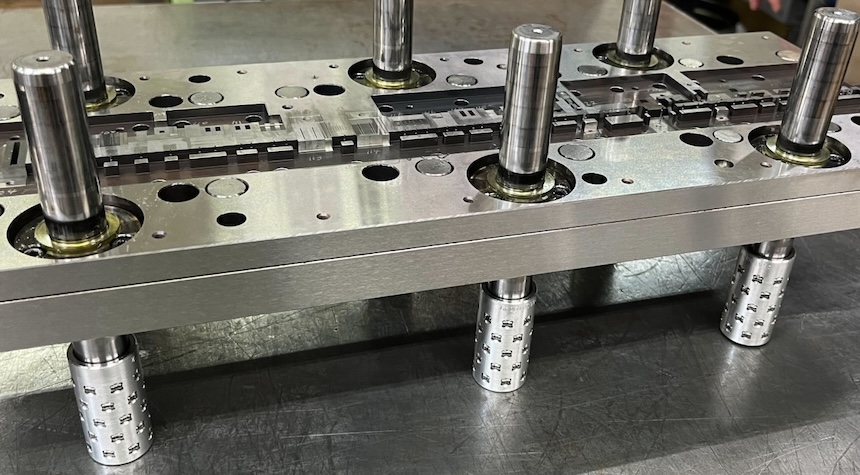
Innovation as a success factor
Yoshio Kanazawa, Deputy Head of the Design Department of the technical division, explains that one of the company's strengths is «to develop solutions to challenges in processing techniques and methods that were not previously available on the market in response to customer requests». Examples of this include the processing of thin materials with a thickness of just 25 μm, the processing of plastics for credit or bank cards and the deep-drawing of extremely small parts. Deep drawing in particular requires a unique technology in order to be able to produce the desired end connectors from a very small blank of a special material. To further develop these strengths, the company set up its own «Development and Improvement Department» within the design department in April 2023 to promote technical innovations. The various departments in the company – for production, technology and sales – work closely together to utilize the strengths of the respective teams and thus enable further growth.
Problems due to insufficient rigidity of the tooling guide elements...
The company's existing high-speed presses can achieve up to more than 1,500 strokes per minute, depending on the product. However, in order to be able to reliably maintain a processing accuracy in the micrometer (μm) range, stricter criteria than before had to be applied when procuring the guide elements used for punching tool production. The problems that arose with fluctuating product quality on the one hand and reduced productivity on the other were solved by changing the supplier.
The defects were discovered after it became apparent that the previous procedure for tool manufacture was not sufficient to ensure trouble-free production. The cutting clearance between the punch and die is checked and adjusted during acceptance after the manufacturing of a new tool. However, after clamping into a press, tools with previously used guides showed that the dimensions of the cutting clearance determined that they did not match the values specified by the design department. During production, it was also discovered that the clearance between the punch and die deviated every time the tool was clamped in a different press. As a result, the product was out of tolerance and the reject rate increased.
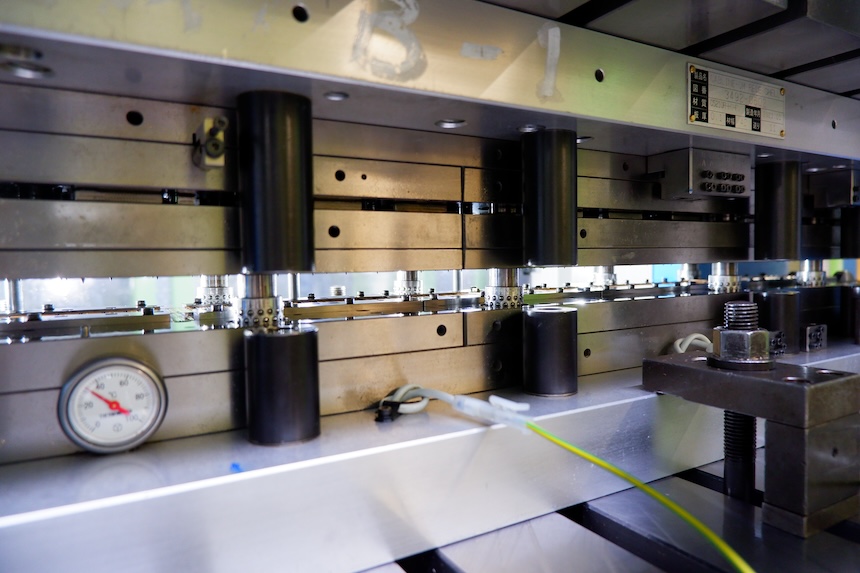
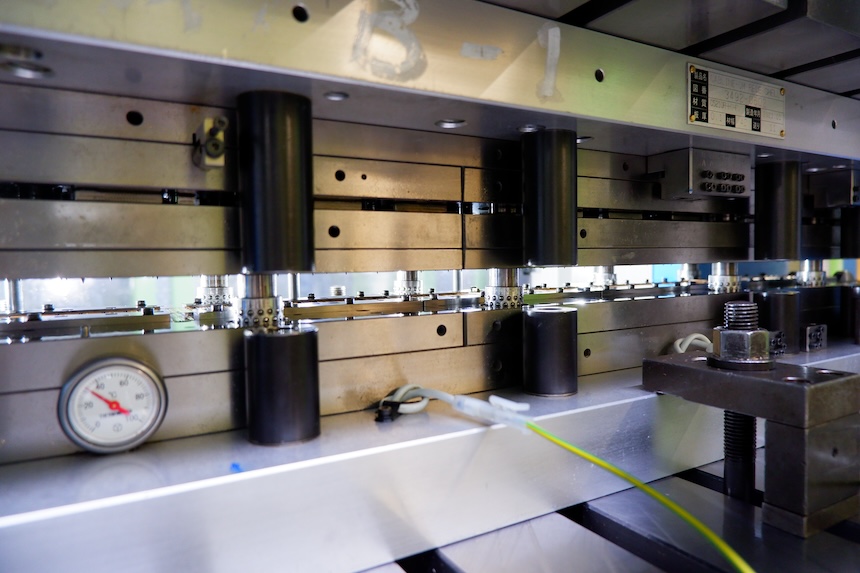
...were solved by changing to Agathon guides
To solve these problems, the sliding guides previously used were replaced by roller cage guides from the Swiss manufacturer Agathon. Agathon is a precision machine manufacturer with over 100 years of history that specializes in high-precision parts for stamping and injection mold tools and enjoys an excellent reputation on the global market. Its top products include backlash-free preloaded guide systems with roller cages.
The rollers, which are manufactured with the highest precision, have a larger contact area with the guide pillar or bushings compared to balls. An equally important factor for Ichimura was the transition to the center flange pillars, which are firmly bolted to the guide plate. The smooth straight pillars used to date were merely pressed in. Therefore, when subjected to 5
shear forces, they behave like a centrally loaded beam resting on two supports. In contrast, the two «pins» of the Agathon pillar, which are fixed to the middle flange pillar, behave like much shorter beams that are firmly anchored on one side. The rigidity of the tool structure against the effect of transverse forces is therefore much greater. The result is particularly high precision combined with maximum rigidity.
After using the Agathon guides, it became apparent that the previous damage and signs of wear on the bushings and cages were reduced to almost zero. The product quality and the lifespan of the tools increased significantly, while the amount of maintenance and assembly work required when changing tools decreased considerably.
«In the past, we always had to make adjustments to the cutting elements when reclamping the tools, but after switching to the new guides, this is hardly necessary anymore»
Koji Wachi, Leiter der Technologieabteilung bei Ichimura Seisakusho
«There used to be more than ten people involved in tool maintenance, but after the switch to the new guides, that number dropped to a handful. I think the biggest success of the changeover is that the labor saved is now being used productively in other areas»
Takuya Hoshino, stellvertretender Leiter der Technologieabteilung bei Ichimura Seisakusho
Aiming for an image as a «proactive» company
The company is currently focusing on further developing its human resources. Progress is being made, for example, in the training of «technical» salespeople, i.e. salespeople who understand technology. «We have introduced a corporate culture in which employees rotate between production and sales every three to five years», says Hiroshi Wachi, head of the sales department. In a market environment where, according to Deputy CEO Hoshino, «a sense of speed is of the utmost importance», the ability to answer technical questions at the point of sale is proving to be a major strength of the company.
According to CEO Satoru Ichimura, the company also strives to create an image for its customers that can be described as follows: It wants to be perceived as a «proactive» company. This means not resorting to excuses when dealing with customer inquiries, but rather doing everything possible to outperform the competition through better technology. To this end, he wants to support the sales staff with products of the highest quality and motivate them to constantly strive for further improvements. Market analysts anticipate that demand for electronic components will continue to rise in the future as electromobility advances and automation increases. The company is systematically preparing to be able to respond to this proactively.