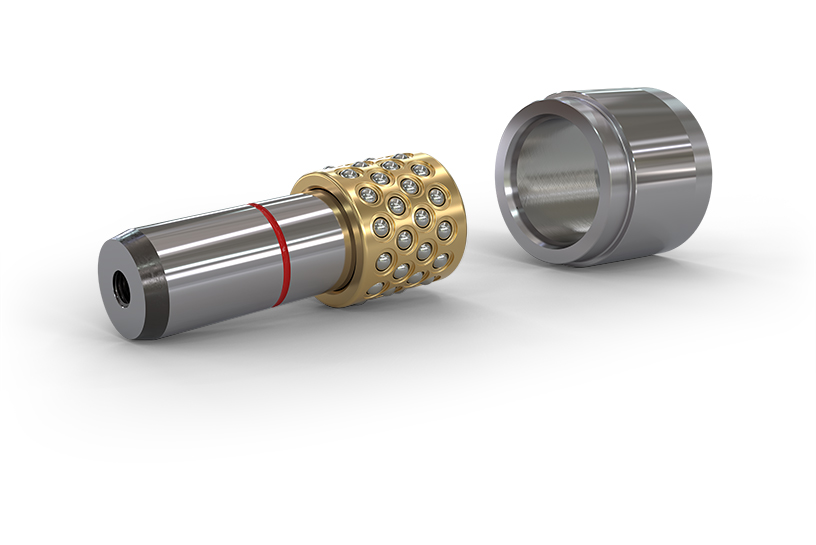
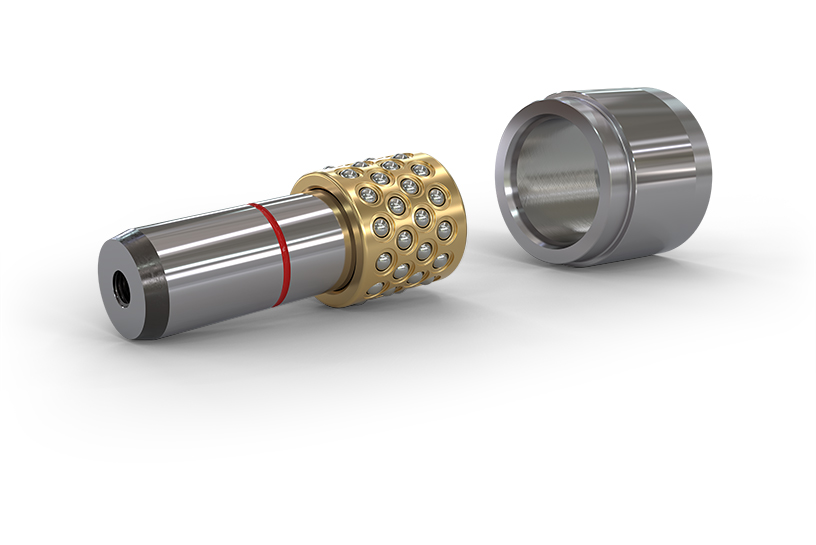
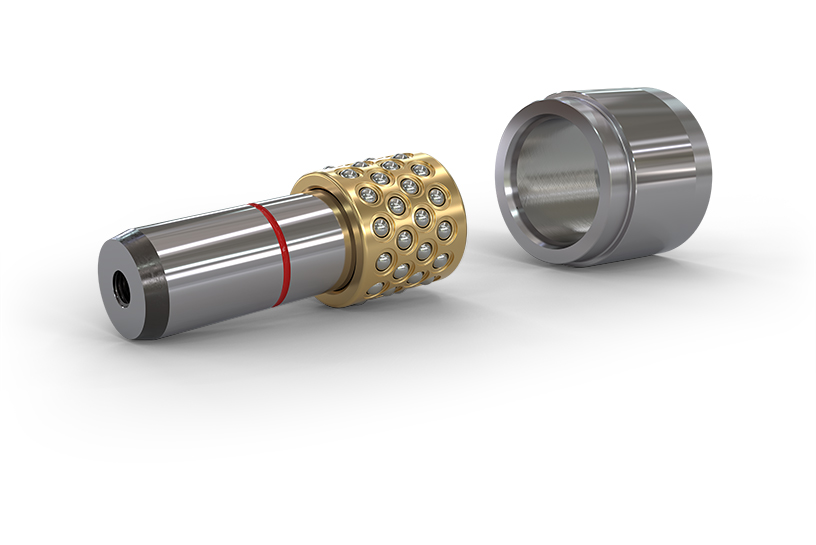
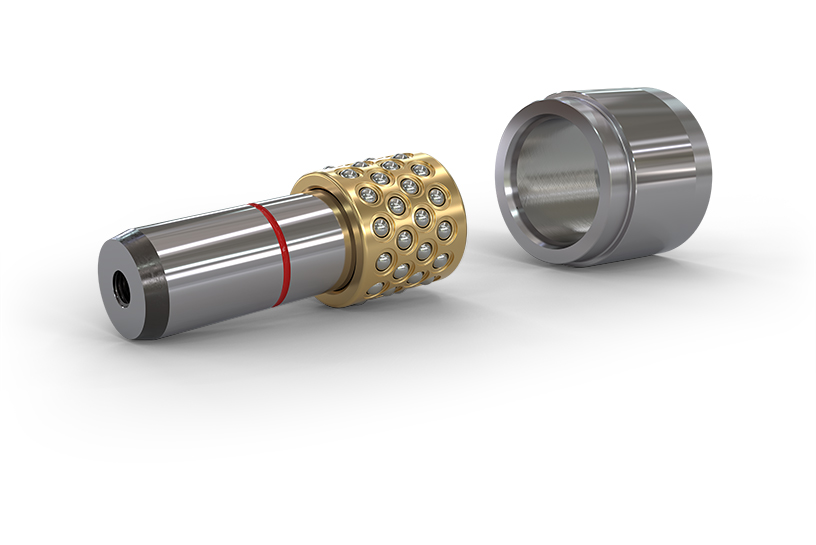
WESA AG successfully uses the Agathon Mini Fine Centering system
WESA AG from Inkwil has been producing high-quality injection molded parts in thermoplastics and thermosets for over 60 years. The company aims to achieve high customer satisfaction through professional competence, high quality, adherence to delivery dates and fair prices. Customers from the medical and linear technology sector as well as the mechanical, electrical and armaments industries receive everything from one source and are individually supported by WESA. Therefore, the motto of WESA is also «not simply injecting plastic parts, but finding innovative solutions and supporting the entire process chain, for small series up to complex assemblies». WESA AG is specialized in the production of small parts up to approx. 100 grams of injection weight or 0.1 to 80g part weight, which are produced in small series from 2'000 pieces as well as in large series with up to 1 million pieces over several years. After the development and launch of the Agathon Fine Centering systems in 2010, WESA has been a regular customer of the Bellach-based company. Yves Ulrich, Design and Project Manager at WESA, explains the reasons for this: «Prior to using Agathon’s Fine Centering systems, we worked with flat centering systems from an Agathon competitor for pocket-shaped processing. The disadvantage of this solution was that the pocket often had to be manufactured in a further clamping. This procedure takes a lot of time, involves the risk of clamping errors and is far less precise than the current solution». Since the introduction of Agathon Fine Centering systems, WESA has been able to produce injection molds and the location hole for centering 2 in one clamping. In 2019, Agathon also launched the new Mini Fine entering system, which was developed in part due to Yves Ulrich’s need for smaller centering dimensions. Just in time for an upcoming project.
Challenging project
In November 2019, WESA received an inquiry from a customer in the machine industry for the production of a component which was needed in a quantity of 200'000 pieces per year for the production of a grease dispenser. In total, WESA had to guarantee a production rate of 1.25 million cycles or 5 million units. As part of the quotation process, the part to be produced was analyzed and it was clarified whether and how it was to be produced by injection molding. Flow analyses were also a part of this phase and their findings were taken into account in the offer. Based on this, WESA was able to provide input regarding differences in wall thickness (thick wall), which led to an article change. In January WESA was awarded the contract and Yves Ulrich immediately started to develop the mold on the basis of the customer’s defined requirements regarding tolerances, surfaces, injection points, dimensional accuracy and ejection marks. With a great deal of know-how and experience, all parameters such as size, design and positions were defined during the design phase. Finally, at the end of April, the sampling process including the creation of the initial sample report took place. As soon as the customer had checked and approved the parts, production began.
Provisional solutions
Before Yves Ulrich was able to use Agathon Mini Fine Centering system, manual work was required: purchased standard pillars had to be measured, reworked and fitted to the holes in the plate as paired sliding guides. This complex procedure did not meet the requirements in terms of zero backlash – only a backlash range of 4 μm was achieved – and also in terms of durability. A further drop of bitterness was the high wear of the sliding guides that led to a rapid wear of the bore, which is why the bore had to be reworked and a special pillar with a new diameter had to be produced. In order to remedy this, Yves Ulrich and his team used oversized special pillars, which had to be produced at great expense, so that the entire mold did not have to be rebuilt. With Agathon Mini Fine Centering system, WESA now has a standardized and ready-toinstall solution that considerably reduces the effort involved and sets new standards in terms of zero backlash and service life.
The Agathon Mini Fine Centering in use
The part to be produced by WESA in the present project has two movable shutters and requires a 4-cavity injection mold. Because the plate integrated in the mold springs back during production, there was a risk that it would be jammed or crushed, thus destroying the two shutters. This function is not monitored in the mold, which is why it was a defined goal to keep the core puller running smoothly and thus preventing the production of reject parts. This was achieved through internal guiding of the plate instead of a sliding guide/flat centering from outside. So this project was not about centering in the true sense of the word, but about the play-free guidance of a short-stroke application that centers the plate instead of the mold and prevents the slip stick of the sliding guide. WESA’s Design Manager adds: «I knew that we had a problem with jamming and tilting and I thought about how to solve it. That’s how I came up with the idea of guiding the core puller or the sprue plate
precisely and without play. So I had only to find out how big the centering to be used may be and order the corresponding model A-7980 – in this case without bushing – from Agathon».
Mini Fine Centering with or without bushing: Tips from the experts
The choice and heat treatment of the material from which the tool is manufactured is of course of major importance. Yves Ulrich uses wear-resistant steel up to 60 HRC especially for the production of parts made of plastic with additives. Also with the aim of producing tools that are as durable and wear-free as possible. Stefan Nobs, Technical Manager in the Agathon Standards Team, continues: «In order for the Agathon Mini Fine Centering system to be used without bushing – i.e. when the customer manufactures the counter-rolling surface himself – the plate hardness should be at least 56 HRC. The harder the plate, the better the performance and service life of the centering device. In the case of the WESA project, ideally a high-quality tool steel 1.2379 was used and through-hardened with 60 HRC. The diameter of the counter-rolling surface
was manufactured with the intended tolerance by WESA itself, according to the specifications in the Agathon product brochure».
Economic considerations
For economic reasons, injection molding part manufacturers – including WESA – strive to use the smallest possible injection molding machines, which is why the clamping surface for the mold is often limited. Therefore, there is usually not enough space available for the flat centering devices used in the past – normally 4 pieces at the edge of the plates. With the Agathon Mini Fine Centering units, which can be used anywhere on the plates, this problem has virtually solved itself and there are no longer any limits to design freedom. «In the end, this new development saves us time and money and we achieve a
ROI almost immediately», Yves Ulrich is happy to report.
Impressive quality
When you ask Yves Ulrich what makes Agathon different from other suppliers, you get a clear answer: «From my point of view, there are no comparable guides or centerings within my field of application. The offer of the other market participants cannot keep up – especially in terms of zero backlash». Precisely because of the backlash-free rolling, in which, unlike sliding, no surfaces are cracked, the Agathon Mini Fine Centering guarantees a very high process reliability and a longer service life. In addition, less lubricant is required, which is of major importance in medical technology, for example. Asked about other advantages, Yves Ulrich says: «Agathon’s Mini Fine Centering systems are excellent for designing». The design depends on the weight of the elements to be centered and the number and size of the centering units to be used can be calculated quickly and easily. «We often replace old guides with new ones from Agathon as part of tool upgrades. This is just a straightforward process, because we already know the product so well», adds Yves Ulrich. All in all, he and his team produce about ten new tools per year, with Agathon Fine Centering units being used in about four of them. It can also happen that WESA asks for advice from Agathon’s specialists. In such cases Yves Ulrich sends his tool to Agathon as a CAD drawing and lets his supplier find out how the parts can be implemented. An entirely satisfying cooperation for both sides.