System guide pillar
Standard: 6701 Ø15
High-precision plug & play solution for maximum flexibility and durability. In combination with the roller bushing system, the system guide pillar combines guiding and centering in just one assembly.
Advantages
- Available diameters 15, 25, 32 and 40 mm with installation diameters 30, 42, 54 and 66 mm
- Additional plates can be guided on the same main guide
- Several plate thicknesses can be covered thanks to the adjustable retaining ring
- Can be combined with all ball and roller cages and plain bushes from the Agathon product range
- Patented product: more info see here https://www.agathon.com/patents
Guidance and centering
Guiding and centering concept
- Combination of two different systems in the mold
- The guide pillars only take over the coarse alignment of the mold during most of the closing movement
- Only in the last millimeters of the closing stroke do flat centering devices take over the fine alignment
- This can cause problems with long, spotting or sensitive mold areas
- The flat guides are subject to relatively high wear
- The Agathon Guiding System Plus performs all guiding and centering tasks over almost the entire closing stroke with just one assembly
- Smooth-running and highly precise guidance due to preloaded profile roller cage
- No jerky sliding during mold movements
- Extremely easy handling: low-maintenance, durable, no pairing required despite roller guide
- Virtually wear-free
Conventional approach
The Agathon concept
Cost benefits
Advantages of the Agathon concept
- Four main guides and four flat centering devices are required
- The production of the pockets for flat centering is complex, time-consuming and imprecise
- Two systems in the tool require valuable space
- Precision depends on manufacturing tolerances and wear condition of the guide and centering elements
- High lubricant and maintenance requirements
- Dirt ingress due to abrasion and particle formation
- Guiding and centering combined in a single assembly
- Pocket production for flat centering is no longer necessary, which saves time and costs
- Enlargement of the working area by up to approx. 30 % for additional cavities, slides or temperature control
- Precision remains at the highest level over the entire service life thanks to backlash-free preloaded guide with profile rollers
- Low lubricant and maintenance requirements increase the productivity of the system, reduce maintenance costs and protect the environment
Previous approach
The Agathon concept
Product features
Key features and highlights
- The pillar can be adapted to different plate thicknesses by positioning the retaining ring accordingly
- The ring, which can be reordered as a spare part, can be used with rolling bearing system 7231 and system guide pillar 6701
- Secure fixing thanks to heat-resistant O-ring (up to 200 °C)
- Tool is already centered well before complete closure
- Abrasion on spotting surfaces and plunger cores is prevented
- Tool life is significantly increased
- Minimum quantity lubrication is sufficient
- Roller bushing with brass profile roller cage allows cleaning in an ultrasonic bath and temperatures up to 170 °C
- Ideal for clean room, high-precision, micro injection molding and high-temperature applications
- Significantly higher travel speeds and therefore higher production output possible
Retaining ring (standard 8005) enables adaptation to different plate thicknesses:
Long centering path:
Optimized for high-end applications:
Advantages of the Agathon Guiding System Plus
Advantages at a glance
- Thanks to this concept, only one size is required in stock. The guide can continue to be used if the tool and plate thicknesses are changed
- Compatibility: retrofitting to tools is possible without reworking the inserts
- No pairing required: Each system guide pillar standard 6701 from the Agathon product range can be combined with bushing of the same diameter as standard 7231. Attention: Do not exceed length l2max
- Spare parts available from stock
- The division of tasks between pillar guide and flat centering is eliminated
- Simplification of the tools: Fewer components and less space required on the clamping surface, significantly lower production and assembly costs
- This means more cavities and higher productivity on the same clamping surface
- Existing flat centering devices can be removed when retrofitting the Agathon Guiding System Plus
- Backlash-free preloaded guide with profile roller cage ensures maximum precision and part quality over the entire service life of the tool
- The service life is 5-12 times longer compared to conventional systems
- High process reliability avoids rejects and production stops
- Lower maintenance requirements and higher productivity
Flexibility thanks to adaptability to different plate thicknesses using a retaining ring:
Better utilization of the clamping surface:
Longer service life and greater precision:
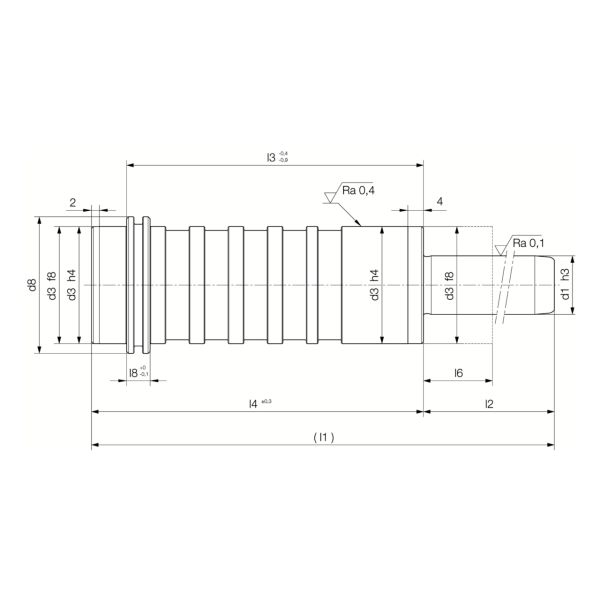
Lieferumfang: inkl. 1 Ringbride Norm 8005 im jeweiligen Durchmesser Material: 100Cr6, gehärtet 62-64 HRC, randschichtgehärtet, Tiefe 1.5+1 mm Temperaturbeständigkeit: bis ca. 170°C
Technical data
d1
=
Pillar diameter, tolerance h3, precision ground
d3
=
Outer diameter of the guide pillar for fit h4/H5(H6)
d8
=
Outer diameter of the retaining ring (flexible collar)
l1
=
Overall length of the guide pillar
l2
=
Length of the diameter d1
l3
=
Mounting positions of the retaining ring (flexible collar)
l4
=
Length of the mounting diameter d3
l6 (mm)
=
Permissible thickness of lifting plates
l8
=
Width of the retaining ring
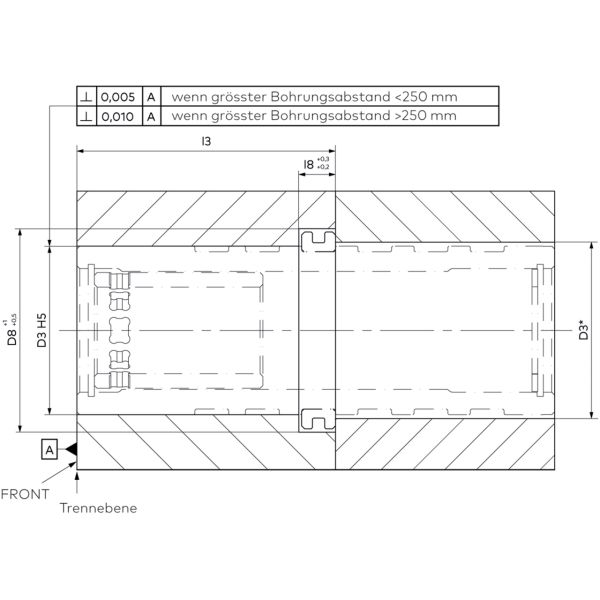
Dimensional drawing Installation tolerances
Accuracy requirements
- The pillar and bushing are installed in bores with tolerance H5
- Alternatively, tolerance H6 can be used for lower accuracy requirements
- Pay attention to the installation direction
- If the largest hole spacing of the main pillar is less than 250 mm, the perpendicularity of the mounting hole to the parting plane should be <0.005 mm per 100 mm length of the guide pillars.
- If the largest hole spacing of the main pillar is greater than 250 mm, the perpendicularity of the locating hole to the parting plane should be <0.010 mm per 100 mm length of the guide pillars.
Position tolerances: - If the largest hole spacing of the main pillar is less than 250 mm, the positional accuracy should be <0.01 mm (i.e. ±0.005 mm)
- If the largest hole spacing of the main pillar is greater than 250 mm, the positioning accuracy should be <0.02 mm (i.e. ±0.01 mm)
- Recommendation for best performance: finish pre-drilled plates with grinding allowance to the desired tolerance or have plates produced with the recommended tolerance
* = Depending on the required accuracy, the following plates can be cut to size for easier installation
Installation tolerances:
Perpendicularity:
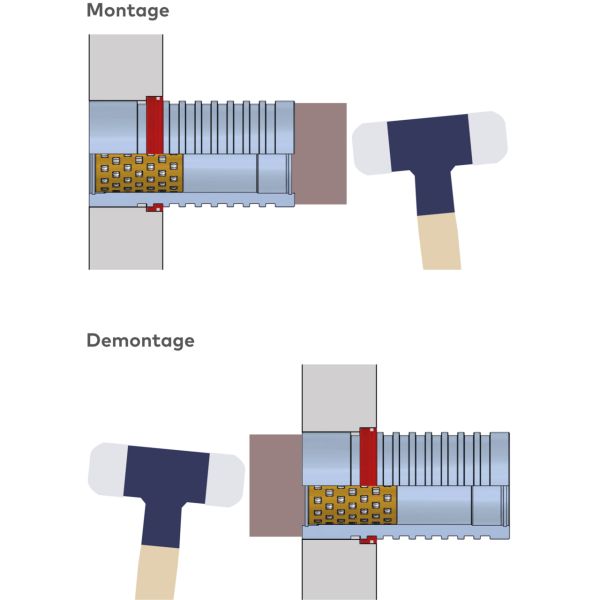
Image installation and removal
Assembly, disassembly and maintenance of the Guiding System Plus
- Clean and remove corrosion protection before assembly, then lubricate
- Position the retaining ring correctly, insert the O-ring
- Tap lightly into the fit, use a rubber mallet or spacer
- Do not knock on the retaining ring or the ring clamp
- Use a rubber mallet or spacer
- Do not tap the retaining ring, ring clamp or cage
- Do not pull on the ring clamp
- Regularly rotate the bushing and pillar by 60°.
- First remove old grease completely, then apply new grease
- Minimum quantity lubrication is sufficient
- When replacing the O-ring, observe the temperature resistance (FKM)
Assembly:
Dismantling:
Maintenance:
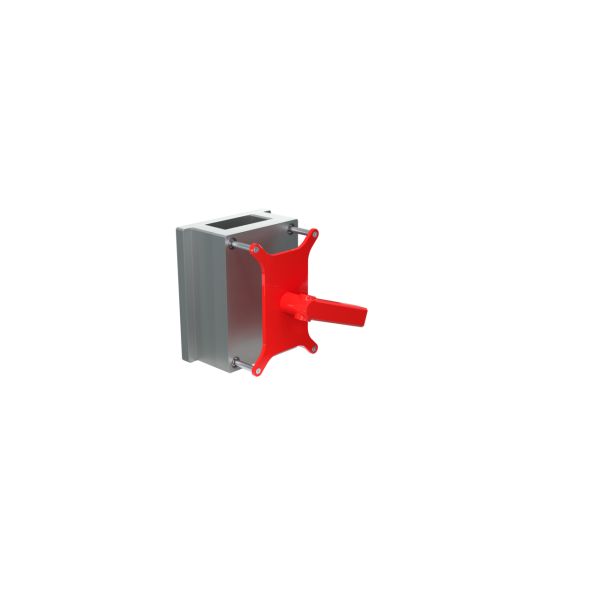
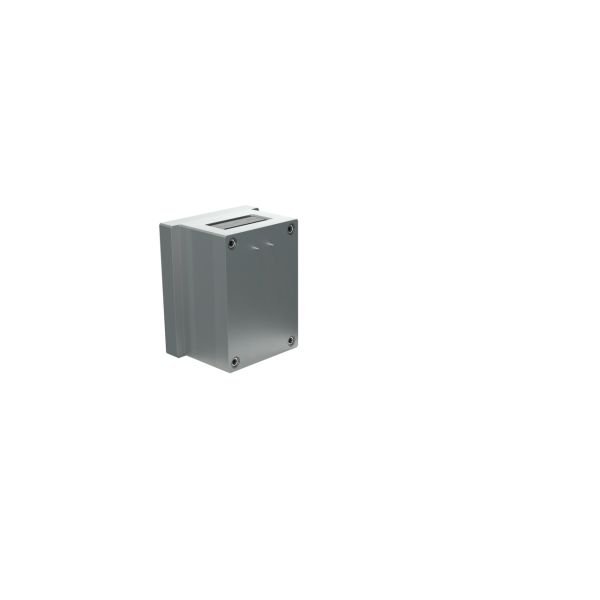
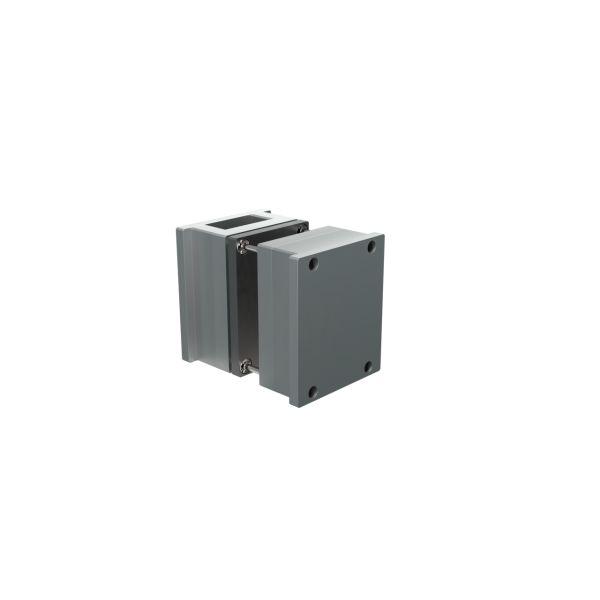
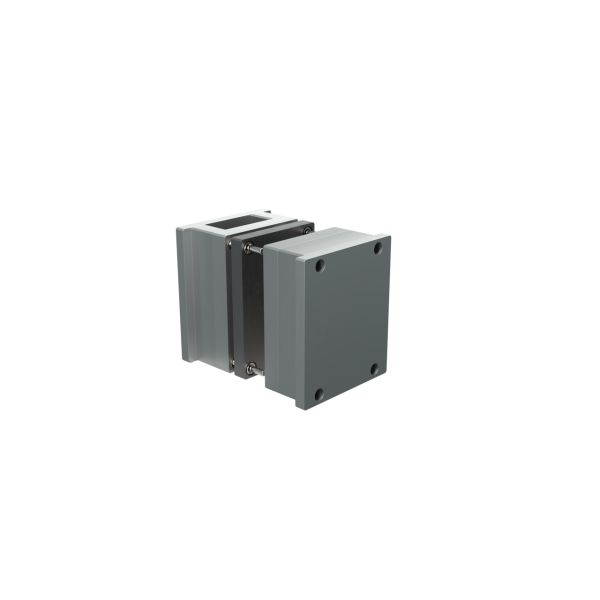
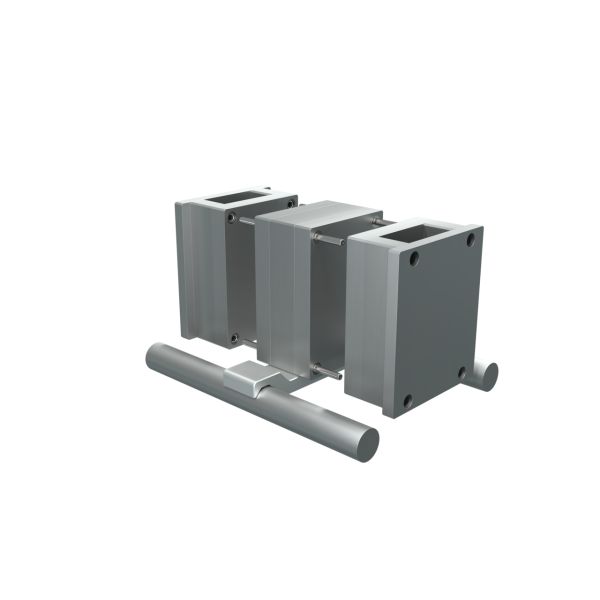
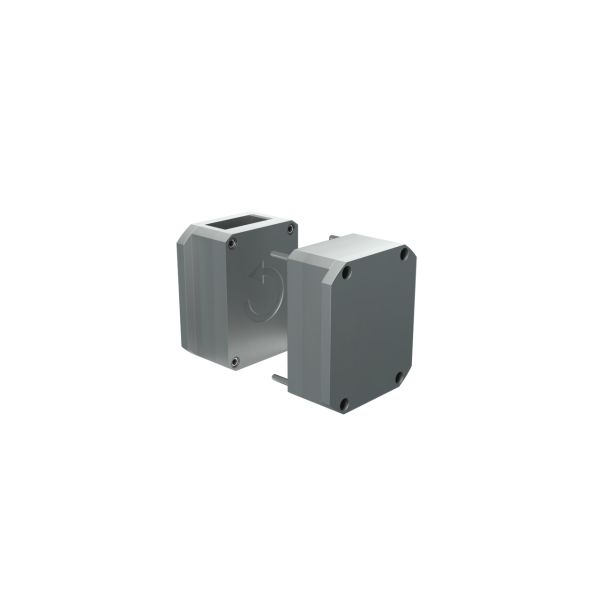
Application type 1 | Center, Lead |
---|