Standard: 656X Ø19
Guide pillar with center flange - for the highest demands and precision
Advantages
- Higher load capacity and rigidity thanks to the integrated collar
- Maximum punching precision, as the high-precision coaxially ground collar surfaces ensure precise vertical alignment
- The low space requirement of the collar enables a compact tool design
- Easy handling/maintenance
- The column can be individually adjusted/shortened
- The higher precision of the structure enables longer tool life
Tool concepts
Stroke accuracy and installation position
Center collar pillars machined to size
The demands placed on stamped parts are constantly increasing, which is why the tool must also meet high standards. In addition, constantly increasing stroke frequencies are forcing the shortest possible strokes, which is why the tools have to be ever more compact. The tighter space conditions make it more difficult to cover the requirements with standardized column lengths alone. In many cases, customized columns are required that are cut to length or precisely manufactured to length. On request, Agathon can manufacture your column in various lengths with tight tolerances. In such cases, L2 and L3 are shortened. This gives the column greater rigidity and the tool correspondingly greater precision.
Installing the guide pillar
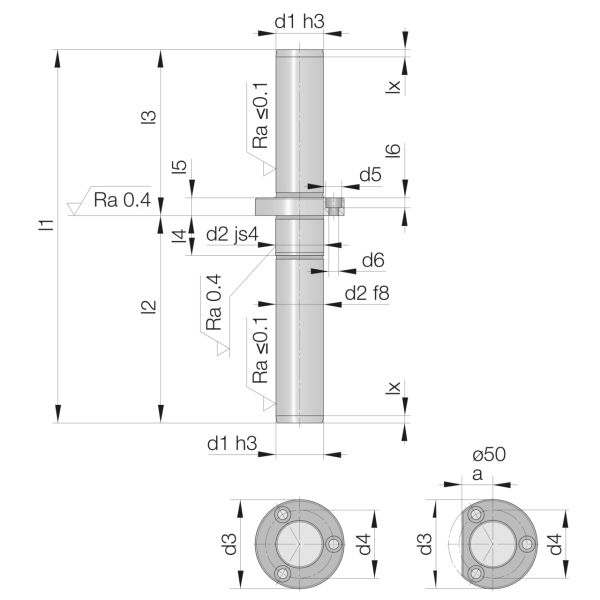
Technical data
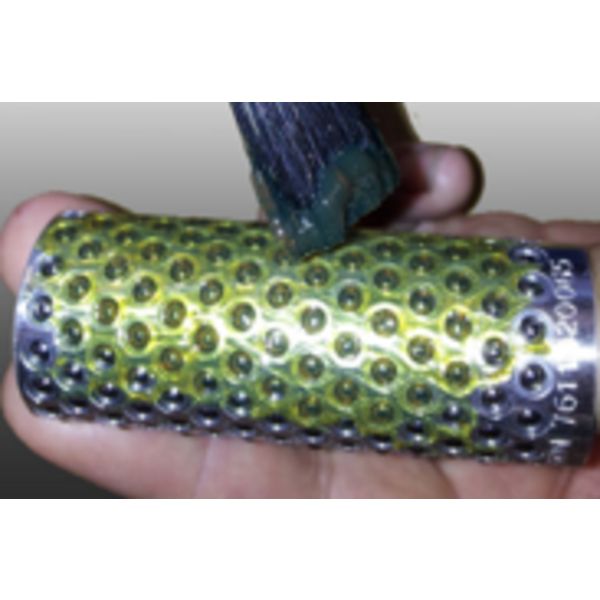
Maintenance and lubrication
Application type 1 | Lead |
---|