Agathon Mini Fine Centering
Standard: 7980 (without bushing)
Guide pillar with ball cage for high-precision and smooth centering processes. For static and dynamic tasks.
Advantages
- Preloaded and therefore backlash-free centering for maximum precision
- Freely positionable with low space requirement
- Smooth and jerk-free movement, minimal wear
- Available in diameters of 8 and 10 mm
- With this pillar unit without guide bushing, the counter-rolling surface is inserted by the user himself
- Alternatively also available as a complete unit with bushing (standard 7981). If required, a separate bushing (standard 7989) is also available
Particularly suitable for: Multi-cavity tools - "dynamic" application
Multi-cavity mold with floating mold insert
Maximum precision for floating mold inserts
- Floating mold inserts are traditionally centered using sliding cubic centering devices. However, centering devices of this type are not backlash-free
- Accommodating cubic centering devices takes up a lot of space and their adjustment is time-consuming. Furthermore, the production of the locating pockets is expensive and imprecise
- The mold inserts are centered backlash-free every time they are closed. Only one of the two inserts is floating
- This is achieved using mini fine centering including ball cages from Agathon
- Centering is smooth and backlash-free with maximum precision thanks to preload
- The mini fine centering devices can be positioned anywhere and take up very little space. This enables a compact, space-saving design of the tool
- Centering bushes can be dispensed with if the mold insert is sufficiently hard. Centering then takes place through a hole in the opposite mold insert
- The small space requirement allows more room for cooling and ejector. This allows up to 30 % more cavities on the same surface area
- Drilling the required holes is more precise and less expensive than producing cubic pockets. The cost saving is up to 50 %
- Instead of four flat centering devices, only at least two fine centering devices are required
Previous approach
The Agathon concept
Comparison of concepts
Advantages of the Agathon concept
- Small footprint, thus more space for cooling and ejector and up to 30% more cavities on the same surface area
- Machining of the holes is more precise and cheaper than pocket machining
- High design freedom: can be placed anywhere on the surface
- Four flat centering devices can be replaced by at least two fine centering devices
- Up to 50% cost and 30% space savings thanks to simpler machining and smaller installation space
Variant injection molding
Center quick-change mold inserts
- In order to fit mold inserts into the master mold with high precision, pockets and inserts had to be machined in a complex process
- Changing mold inserts was complicated, time-consuming and only possible with special expertise
- Mold inserts and master mold are connected via a plug-in connection
- Mini fine centering devices from Agathon serve as plug-in connectors
- In this way, mold inserts can be easily rolled off and centered without play and thus with high precision
- In addition, the change can be carried out quickly and without jamming, even without special know-how
- If the material of the mold insert is sufficiently hard, centering bushes can be dispensed with. The centering pillar and ball cage are held directly by the opposite mold insert
Previous approach
The Agathon concept
Positioning concepts in comparison
Advantages of the Agathon concept
- Repetitive centering accuracy < 0.26µm
- Gentle and easy assembly and disassembly
- Smooth-running without jerky sliding
- Significantly reduced assembly time
- Plates cannot tilt. The precision of the mounting hole is maintained
- Assembly can optionally be carried out without bushing and thus save even more space - apply the diameter tolerance d2 statically for self-made mating surfaces
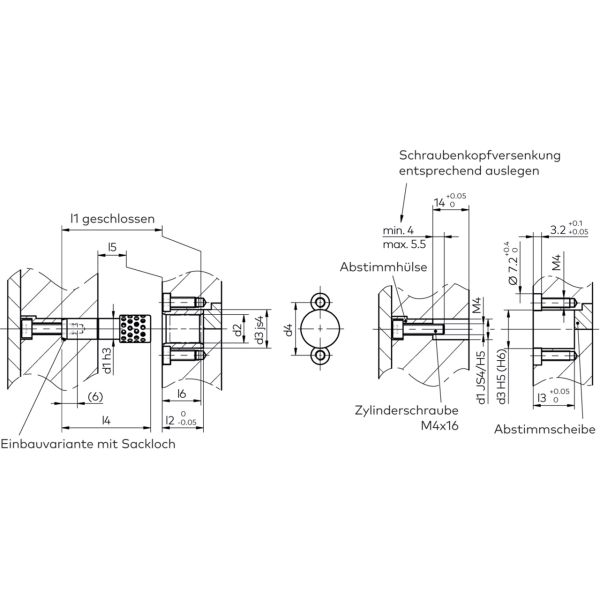
Supplied with: 1x M4x16 (A-07000180), 2x M4x8 (A-07007530) Material of balls: 100Cr6 - 1.3505, hardened 62 to 64 HRC; Centering column material: 16MnCr5, hardened 61 to 63 HRC.
Technical data
d1
=
Centering pillar l Diameter tolerance ISO h3 l Superfinish ground
d2 dynamisch
=
Outer rolling diameter l Tolerance for in-house production l Dynamic applications
d2 statisch
=
Outer rolling diameter l Tolerance for in-house production l Static applications
l1
=
Nominal length of the closed fine centering l including from cage end l collapsed
l4
=
Total length of the fine centering
l5
=
Entry into the centering (preload), or guided distance
l6 (mm)
=
Immersion depth of the centering
Entrance C
=
Basic dynamic load rating in N - Initial load capacity
Closed C0
=
Basic static load rating in N - Tool closed
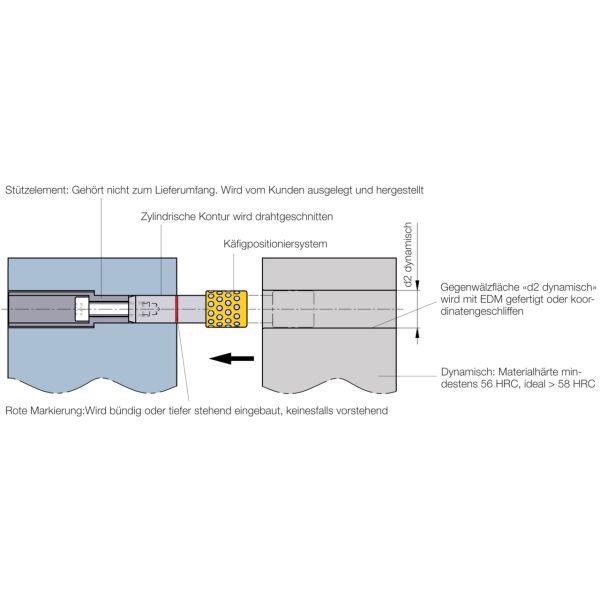
Dynamic installation variant
Dynamic application
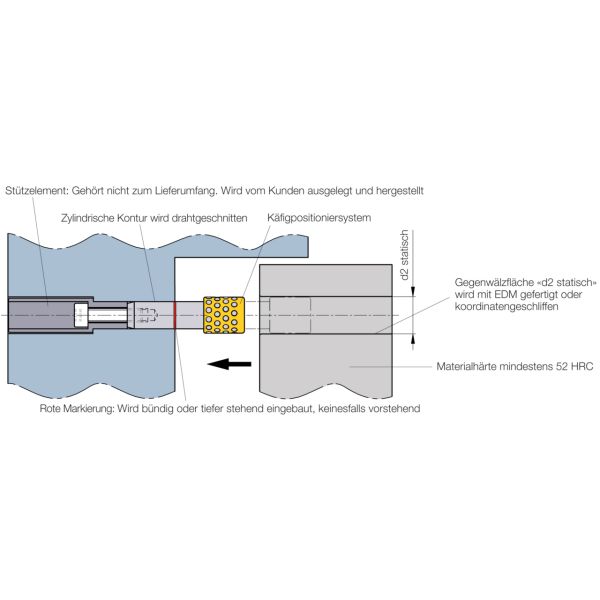
Static installation variant
Static application
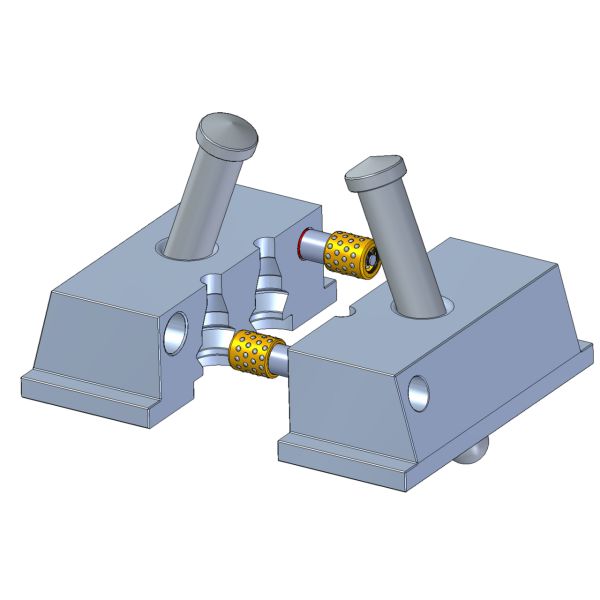
Slide and jaw centering
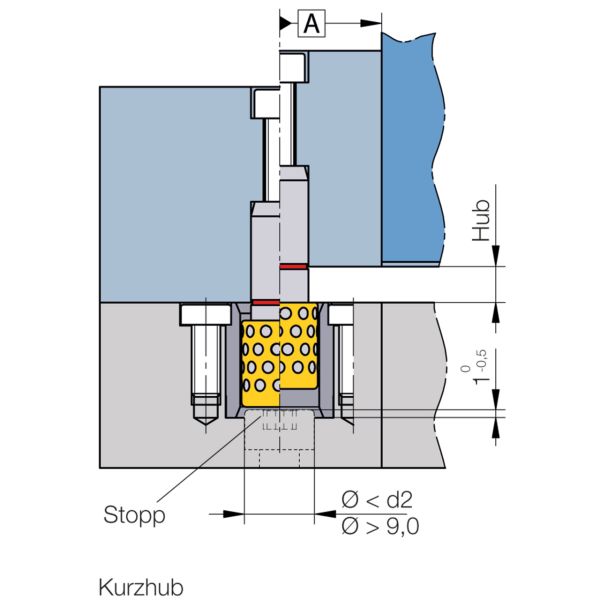
Short stroke
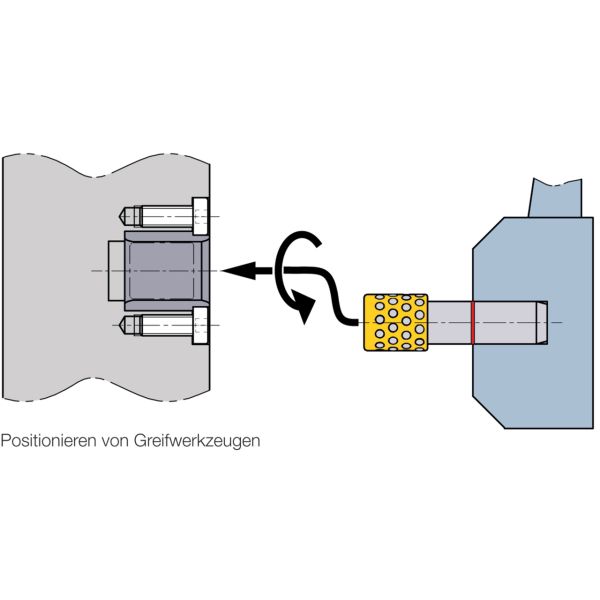
Positioning of gripping tools
Application type 1 | Center, Quick change |
---|