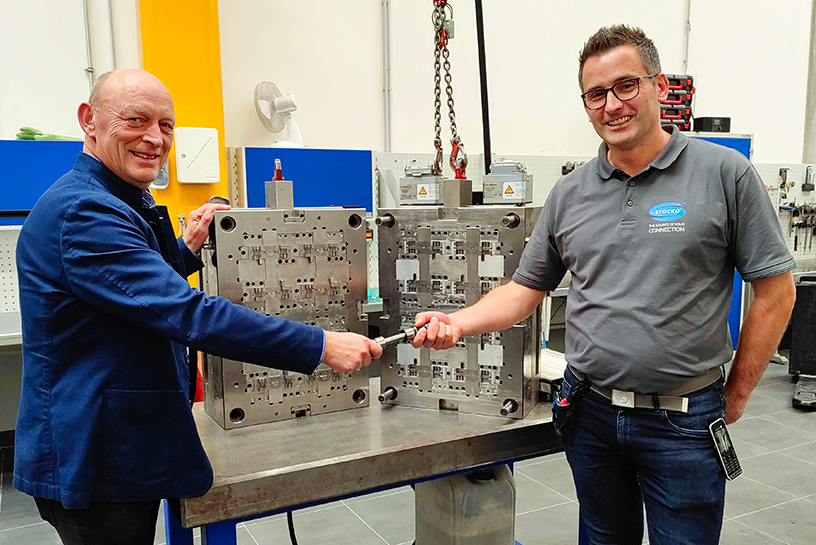
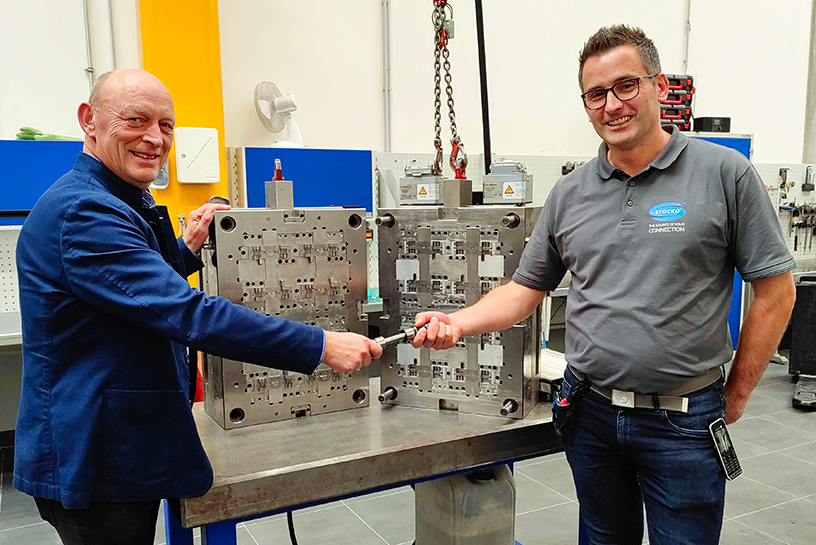
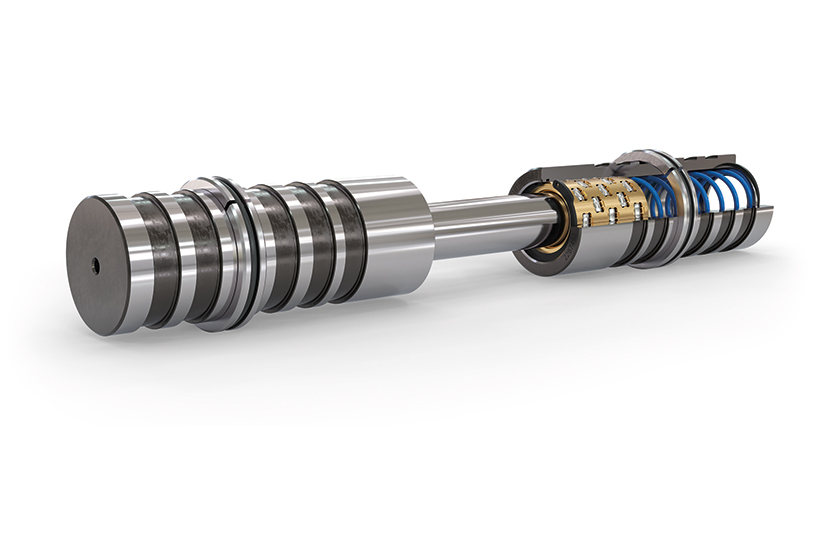
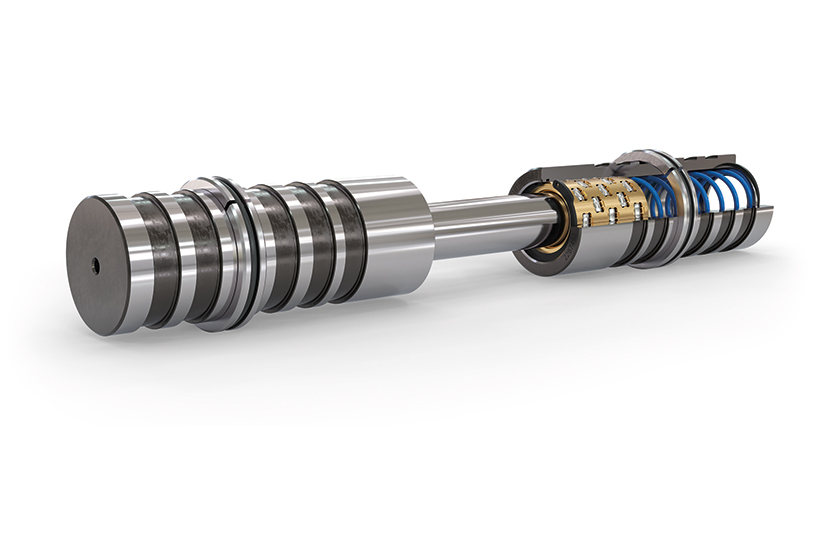
Hochpräzise, langlebig und kosteneffizient
Beim Schliessen der Spritzgiessform kommen traditionell gleich zwei unterschiedliche Zentriersysteme zum Einsatz: An den Ecken der Form sorgen vier Führungssäulen zu Beginn der Schliessbewegung für eine eher grobe Vorzentrierung, während erst auf dem letzten Teilstück zusätzlich vier Flachzentrierungen an den Formseiten die Feinzentrierung übernehmen. Sind wirklich zwei Systeme erforderlich, die zudem nicht optimal harmonieren? Ein Gespräch mit dem Leiter der Werkzeuginstandhaltung des Steckverbinder-Herstellers Stocko Contact über seine Erfahrungen mit der einstufigen und zugleich hochpräzisen Agathon-Systemführung Plus.
«Wir sind Hersteller von Steckverbindersystemen für Industriebranchen wie die Hausgeräte- und Heizungstechnik oder die Automobilindustrie», sagt Oliver Müller, Leiter Werkzeug-Service der Stocko Contact GmbH & Co. KG in Hellenthal (Deutschland). Bei diesen Verbindern kommen unterschiedliche Technologien wie Schneidklemm-, Crimp- oder Lötanschlüsse zum Einsatz. Dabei setze Stocko auf solide Lösungen, hohe Qualität und vielfältige Einsatzmöglichkeiten. Angesichts von Marktbegleitern, die teils vielfach größer sind, setze das Unternehmen vor allem auf Innovationsfähigkeit, Flexibilität und Entwicklungspartnerschaft bei der Findung von Lösungen für neue Herausforderungen am Markt. Zunehmende Funktionsdichte und Miniaturisierung führten dazu, dass bestehende Artikel für spezielle Anwendungen nach und nach seltener eingesetzt werden. Stattdessen verlangten die Kunden zunehmend individuelle Anpassungen oder Neuentwicklungen. Hier setze Stocko auf das Know-how, den Weitblick und den Pragmatismus seiner Entwickler bei der Findung von Lösungen, die sowohl technisch darstellbar als auch wirtschaftlich sinnvoll sind.
Im Spritzguss im Hellenthal produzieren 80 Maschinen täglich 2,7 Mio. Gehäuse für Steckverbinder mit Gewichten zwischen 0,1 und 16 Gramm.
Erhöhte Anforderungen an die Produktionswerkzeuge
«Diese höheren Anforderungen an die Produkte lassen sich nur mithilfe entsprechend leistungsfähiger Werkzeuge erfüllen», ergänzt Oliver Müller. Dies gilt sowohl für die in der Stanzteileproduktion eingesetzten Folgeverbundwerkzeuge als auch für die Spritzgiessformen. Während die Folgeverbundwerkzeuge überwiegend extern bezogen werden, erfolgt die Herstellung der Spritzgiessformen im eigenen Unternehmen. Sie sind äußerst aufwendig und bestehen aus hunderten oder gar tausenden Einzelteilen. Viele davon sind sehr filigran. Um die einwandfreie Funktion der mit diesen Formen hergestellten Steckverbinder und Kontakte sicherzustellen, müssen sie mit höchster Präzision gefertigt werden. Bei ihrer Produktion wird deshalb der bestmögliche Stand der Technik eingesetzt. Dies gilt auch für die Normalien, die für wesentliche Funktionen der Form wie den hochpräzisen Ablauf der Schliessbewegung sorgen. Jede noch so kleine Abweichung beim Zentrieren kann zu Versatz oder Graten an den Bauteilen und damit zu Ausschuss führen. Dabei spielt auch das Langzeitverhalten der Zentrier- und Führungselemente eine wesentliche Rolle, denn die Formen müssen teils etliche Millionen Produktionszyklen absolvieren. Aufwand und Kosten für Wartung und Instandhaltung sind daher ein wesentlicher Faktor. Dies gilt gleichermassen auch für die Folgeverbundwerkzeuge.
Agathon Systemführung Plus statt Flachführungen
«Im Spritzgiess-Formenbau wird die Führung und Zentrierung der Formhälften beim Schliessen traditionell mithilfe von zwei unterschiedlichen Systemen bewerkstelligt: Führungssäulen und Flachführungen», weiß Matthias Rüter, Area Sales Manager der Deutschland-Tochter des Schweizer Präzisionsteile-Herstellers Agathon in Bellach (Schweiz). Die Führungssäulen an den Ecken sorgen dabei für die Grobausrichtung zu Beginn der Schliessbewegung, während vier Flachführungen in der Mitte der seitlichen Formbegrenzung die Feinausrichtung auf den letzten Millimetern des Schliesswegs übernehmen. Die recht kurze Wirkstrecke der Flachführungen kann bei Formen mit engen Abständen bei zugleich stark geneigten Konturpartien zum unerwünschten Tuschieren und damit zu nachteiligen Folgen am Produkt führen. Ebenfalls nachteilig ist der aufgrund der hohen Flächenpressung an den Flachführungen auftretende Verschleiss, wodurch es auch zum «Fressen» der Gleitflächen kommen kann. Bei langlaufenden Formen müssen die Flachführungen deshalb unter Umständen sogar mehrfach ersetzt werden.
Die Agathon Systemführung Plus ersetzt die herkömmliche Kombination aus Führungssäulen und Flachführungen. Dieses „Zwei-in-Eins“-System punktet durch spielfreie, vorgespannte Rollenführungen statt Gleitreibung. Das Ergebnis ist eine langlebige und zugleich hochpräzise Zentrierung schon beim Erreichen der Vorspannung
Als Alternative entwickelte Agathon deshalb die Systemführung Plus. Diese besteht aus präzisionsgeschliffenen Führungssäulen mit Toleranz h3 an den vier Ecken der Form, die in Rollenkäfige mit hochpräzise gefertigten Rollen an der gegenüberliegenden Formhälfte eintauchen. Führungssäulen, Käfige und Rollen sind so genau gefertigt, dass die Führung bereits bei Erreichen der ersten Rollenreihe spielfrei arbeitet. Dank ihres Linienkontakts mit der Führungssäule haben die Rollenwälzkörper mehr als die 6fache Tragkraft und Steifigkeit im Vergleich zu einer Kugel-Säulenführung. Die Formhälften werden somit über nahezu die gesamte Länge des Schliesswegs mit höchster Genauigkeit geführt. Ein weiterer Vorteil ist der geringere Platzbedarf dieser «Zwei in Eins»-Lösung im Vergleich zum traditionellen Ansatz. Das dadurch ermöglichte Weglassen der Flachzentrierung erlaubt wahlweise die Unterbringung zusätzlicher Kavitäten auf der gleichen Fläche oder die Verwendung einer kompakteren Form und damit einer kleineren Maschine bei gleicher Produktionskapazität.
Hervorragende Haltbarkeit
«Wir haben uns im Jahr 2021 erstmals dafür entschieden, die Agathon-Systemführung Plus bei einer Form für Herdanschlussverbindungen einzusetzen, mit der wir Probleme hatten», berichtet Oliver Müller. Da bereits eine langjährige Partnerschaft mit Agathon im Bereich der hochpräzisen Führungssysteme für Folgeverbundwerkzeuge bestand, lag es nahe, sich auch bei diesem Spritzgiesswerkzeug mit der Neuentwicklung von Agathon näher zu befassen. Bei dieser Form mussten früher die Flachführungen aufgrund von erhöhtem Verschleiss nach jeweils etwa 625.000 Spritzzyklen ersetzt werden. Zurückzuführen war dies auch auf die mit 140 °C besonders hohe Werkzeugtemperatur. Der Austausch der bisherigen Flachführungen sowie der bisherigen Führungssäulen gegen vier Agathon Systemführungen Plus erfolgte nach 2,5 Mio. Zyklen. Mit dem neuen System hat die Form seither weitere 1,5 Mio. Spritzzyklen absolviert, ohne dass irgendwelche Beanstandungen im Bereich der Führungen aufgetreten wären.
Leider werde das mit dieser Form produzierte Steckverbindermodell in absehbarer Zukunft auslaufen. Deshalb werde man in diesem Fall wohl keine Chance bekommen, an die tatsächliche Haltbarkeitsgrenze der Agathon-Führung heranzukommen. Aufgrund der bisher gemachten Erfahrungen könne er sich jedoch vorstellen, dass die maximal erreichbare Zykluszahl im zweistelligen Millionenbereich liegen könne. Da die Agathon-Führung kaum mehr koste als die ursprüngliche Ausstattung, habe sich die Investition allein schon wegen der beiden bisher eingesparten Gleitführungs-Sätze mehr als bezahlt gemacht. Hinzu kämen als Boni auch noch die höheren Verfügbarkeiten der Form und der Spritzgiessmaschine, da die Agathon-Systemführung Plus im Unterschied zu den Gleitführungen nicht mehr täglich, sondern vielleicht nur einmal pro Woche geschmiert werden müssen. Zusätzlich zur höheren Verfügbarkeit erspart dies auch die N.i.O.-Teile aus den meist 5-15 Anfahrzyklen, die nach solchen Stillständen erforderlich sind.
Aufgrund dieser guten Erfahrungen seien inzwischen rund 15 Sätze dieser Formführung in andere Formen eingebaut worden. Auch bei diesen Umrüstungen habe es positive Erfahrungen gegeben. Die Zentrierungen erwiesen sich als einfach zu handhaben, wartungsarm und langlebig. Bei weniger lange laufenden Formen gehe er davon aus, dass sich bei Ausmusterung der Form die ausgebauten Systemführungen Plus problemlos in weiteren Formen wiederverwenden liessen. Im Bereich Formwartung hätten die Mitarbeiter positiv angemerkt, dass die leichtgängige Trennung der Formhälften die Arbeit deutlich erleichtere und Schonhammer sowie Montierhebel deutlich weniger zum Einsatz gebracht werden müssten. Auch sei die Minimalmengenschmierung einfach vorzunehmen.
Gute Noten für den Service
«Eine gute Beurteilung kann ich der Firma Agathon auch im Bereich Betreuung und Hilfestellung geben», fasst Oliver Müller seine Erfahrungen zusammen. Bei Fragen oder Problemen habe es stets prompte Unterstützung gegeben, sei es telefonisch, per Teams-Sitzung oder durch einen kurzfristigen vor-Ort-Besuch des Aussendienstes. Im Vergleich mit den Erfahrungen, die er mit anderen Lieferanten gemacht habe, sei dies weit vorne angesiedelt. Nicht nur aus technischen, sondern auch aus wirtschaftlichen Gesichtspunkten sei es überlegenswert, beim Bau neuer Spritzgiesswerkzeuge die Systemführung Plus als Standard vorzusehen.
Die Überwachung der Herstellung und Wartung der Werkzeuge im Formenbau selbst und die Verknüpfung ihrer Betriebsdaten mit den Daten aus der Produktion erfolge in einem sehr hohen Umfang, wobei riesige Datenmengen anfielen. Das Ergebnis sei ein sehr hoher Grad an Beherrschung der laufenden Produktionsprozesse. «Aufgrund meiner Erfahrungen in der Branche kann ich bestätigen, dass das Niveau bei der Betriebsdatenerfassung auf Werkzeugebene bei Stocko Contact vorbildlich ist», bestätigt Matthias Rüter.