Standard: 7611 Ø30
Thanks to its low weight and good thermal conductivity, this universally applicable aluminum ball cage is particularly suitable for high stroke frequencies of up to > 2500 strokes/min. Positioning is facilitated by a mounting aid.
Advantages
- The backlash-free preload (use of columns, balls and bushings with a suitable fit) enables high-precision guidance of the stroke movements
- The tight fitting of rolling elements ensures high load capacity and rigidity
- Patented caulking of the rolling elements ensures a long service life
- Easy handling and maintenance
- Suitable for minimum quantity lubrication
Caulking of the balls (patented)
- Ball is held over a large part of its circumference
- Better holding force of the ball
- Reduced radial ball play
- Significantly reduced jerky load when the rolling element enters the preload
Aluminum ball cage
Stroke path
Definition of preload
Preload is the calculated difference between the inner diameter of the bushing (d2) minus 2x the rolling element diameter (dk), minus the pillar diameter (d1). The result expressed in μm in the minus range is referred to as preload (in relation to the diameter). The individual components must compensate for this value through deflection. The maximum material load capacity up to permanent deformation and thus failure of the component is specified by the Hertzian surface pressure (in our case 4,400 N/mm for ball guides and 4,200 N/mm for roller guides with a linear contact zone).
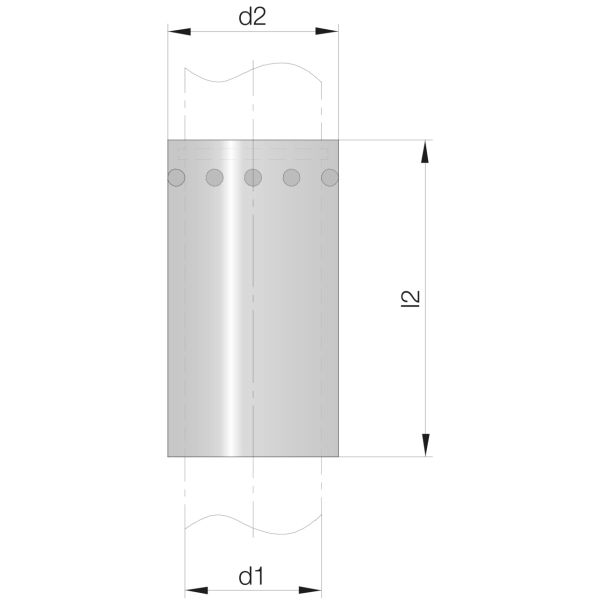
Technical data
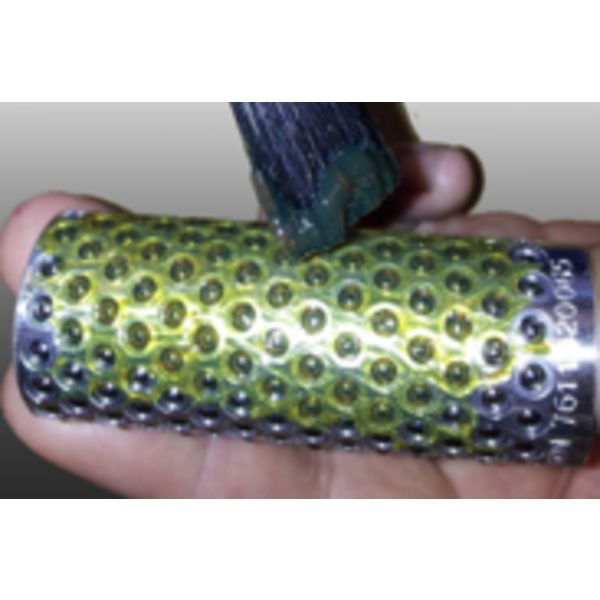
Maintenance and lubrication
Maintenance
● After delivery: Remove rust inhibitor from the centering
● During maintenance: Remove old grease without residue, a washing process is recommended
Lubrication
● Apply new lubricant to the cage of the column guideway
Agathon rolling guides are practically maintenance-free, but a minimum amount of lubrication is required.
The cages are lightly oiled on delivery. They should be washed and lubricated before installation.
Basic lubrication (ball bearing grease with high pressure absorption capacity) before use or during servicing/maintenance increases the service life of the guideway.
Different products can be used depending on the application - a higher quality universal grease is often used.
Use without lubricant is not recommended (e.g. applications in clean rooms, food industry, etc.) - please contact the application technology department for any special solutions.
In the case of extremely high loads and long periods of use, lubricant can also be added periodically during use. Oil is used to flush away any particles/foreign bodies.
Application type 1 | Lead |
---|