Standard: 7992 - Small applications
The smooth-running, rolling Agathon Fine Centering Plus consists of a centering pillar with roller cage. It is used for centering cavities and main parting lines. It ensures very precise guidance and high load-bearing capacity as soon as the first row of rollers is reached. The integrated cage positioning system allows it to be extended from the preload. Manufactured from hardened, wear-resistant roller bearing steel, it is suitable for the mass production of high-precision parts.
Advantages
- Backlash-free and therefore highly precise
- Durability enables use for mass production
- High degree of design freedom for the mold designer thanks to free placement options
- Short cycle times
- High initial load-bearing capacity right from the centering start
- No noticeable abrasion - suitable for clean room production
- Temperature-resistant up to approx. 150 °C
- Low overall costs, also thanks to cost-effective production of the cylindrical locating bore
- Minimum quantity lubrication, therefore little to no maintenance
How is it used...
Advantages of Agathon centering
- Thanks to the precise axial positioning of the roller cage, two rows of rollers are brought into preload in quick succession during the centering start - this ensures a high initial load-bearing capacity and a long service life. The initial load capacity corresponds approximately to the load capacity of 16 rows of balls
- Low wear due to rolling centering. In contrast, with conventional flat centering (cubic centering), the centering start begins with an almost pure line contact. The surface pressure p exceeds the permissible value (pzul) several times over. Only after sufficient overlap of the centering surfaces does the surface pressure fall below a critical value. Only then does a low-wear "gliding" movement occur.
- The service life of the fine centering can be extended by turning the unit by 120 ° -180 ° at a time
- Temperature-resistant up to approx. 150 °C
- Low overall costs, also thanks to cost-effective production of the cylindrical locating bore
- Little to no maintenance, can be used with minimum quantity lubrication
- The designer is free to choose the arrangement and number of fine centering devices installed
Thermal expansion in the injection mold
- Case study: asymmetrically tempered mold, ΔT = 50 K
- Temperature: ejector side 90 °C; nozzle side 40 °C
- Actual offset is reduced by a factor of 3-5 due to heat transfer at the mold parting line!
- Analyzed offset at the separation: 6.2 µm. The Agathon Fine Centering Plus can therefore be used without hesitation
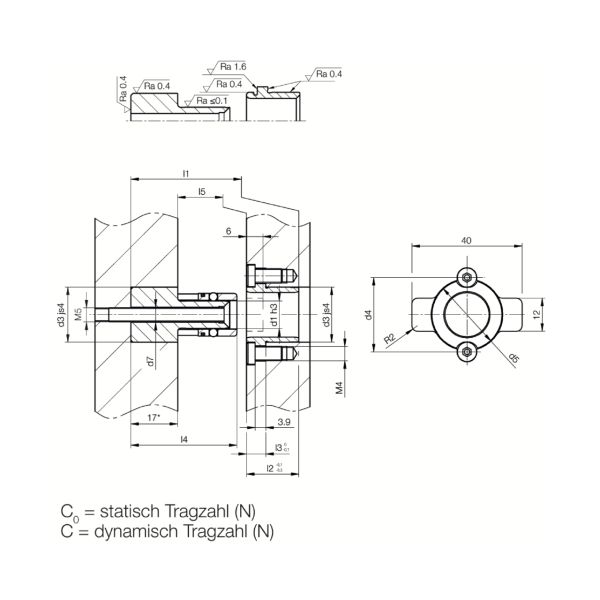
Supplied with: 1x cap screw for guide column and 2x cap screw for guide bush. Materials of bushings, rollers: 100Cr6 - 1.3505, hardened 62 to 64 HRC; centering column: 16MnCr5, hardened 61 to 63 HRC.
Technical data
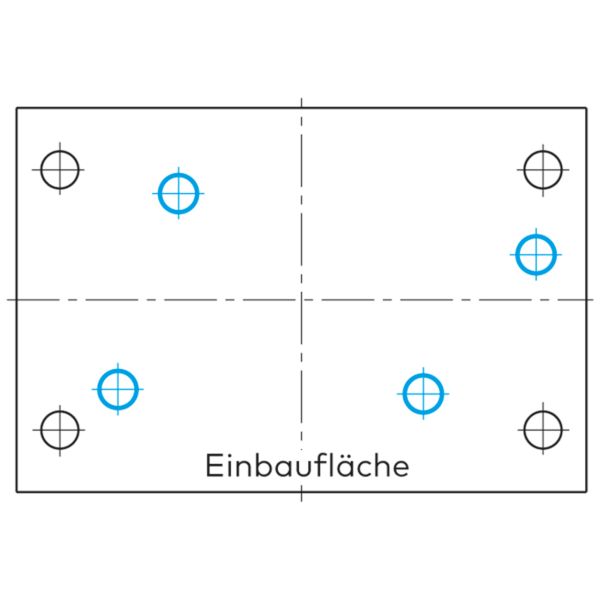
Installation area for Agathon Fine Centering Plus
Accuracies and boundary conditions
Positioning accuracy:
Locating bores for pillar and bushing maximum 0.005 mm positional deviation. The adjustment of the sliding elements must be carried out accordingly on the closed tool so that no radial forces act on the fine centering.
Perpendicularity: Bushing and pillar axis to the tool parting surface maximum 0.005 mm per 100 mm deviation.
Installation depth:
The flatness of all axial bearing surfaces of the bores for the centering units must not vary by more than 0.05 mm.
Boundary conditions: An offset of maximum 0.15 mm can be centered with the fine centering Plus 7992. Ideally < 0.05 mm, pre-centered by the main sliding guide / pillar. Centering bush and centering pillar are matched to each other. Ensure that the two are always installed together as a pair. Solutions for multi-component tools on request.
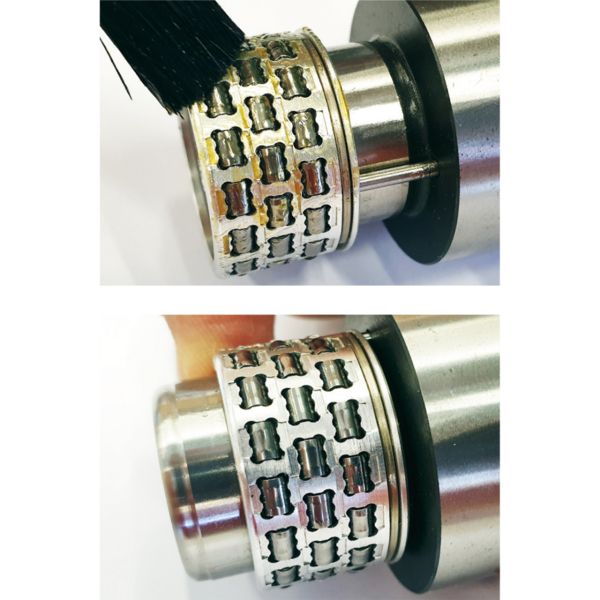
Maintenance Finecentering Plus
Maintenance of the Agathon Fine Centering Plus
- After delivery: Remove rust inhibitor from the fine centering
- During maintenance: Remove old grease without leaving any residue
- Apply new grease to the cage of the fine centering - see catalog for recommendations
- For clean room applications, excess grease can be wiped off with a lint-free cloth
- Centering elements must be replaced if there is no longer any preload. Preventive replacement as part of normal maintenance is advisable
Application type 1 | Center |
---|